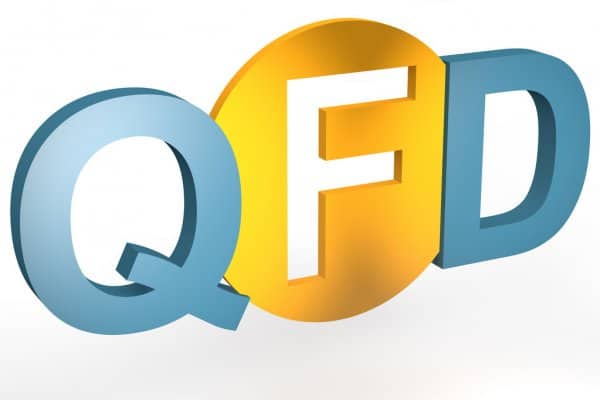
The majority of today’s consumers have a vast array of options available to choose from when it comes to similar products or services. A product’s quality can be assessed in terms of performance, durability, and reliability, and most consumers make their choices based upon a general perception of value and quality.
Quality is a vital parameter that sets an organization or business apart from its market competitors. The Six Sigma Green Belt training Online is a certification course that imparts an understanding of the importance of Quality Control operations in an organization. It focuses on delivering a superior quality product by developing a process-oriented outlook towards Quality Management and encompassing the Total Quality Management (TQM) system. In this context, it is essential to know what is QFD or Quality Function Deployment.
The need for Quality Management
First, let’s address the most pertinent question – what is the need for Quality Management? After all, what is the point of earning a Green Belt training certification without understanding the essence of Quality Management?
So here’s how Quality Management can help your organization grow:
- Quality Management tools assist organizations to design and create products that align with the customer’s wants and desires, guaranteeing the customer’s satisfaction.
- By implementing Quality Management practices in various sectors, including research, sales and marketing, manufacturing, finance and accounting, administration, and equipment maintenance, organizations can ensure reduced costs and increased profits over time.
- Business coverage and data security are not enough to mitigate the possibility of risks. For instance, recalls can lead to financial losses, hurt the brand reputation, and negatively affect the customer’s experience. Hence, businesses must adopt Quality Management practices to minimize the chances of risk.
- When risks are minimized, products will be consistently produced to meet the highest standards of durability, reliability, and performance. As a result, employee morale is boosted with improved performance, increased revenues, and enhanced efficiency.
- Last but not least, a sound Quality Management system helps businesses deliver superior-quality products and maintain a competitive edge while optimizing cost-efficiency and resource utilization.
What is QFD?
Developed in the 1960s by Yoji Akao of Japan, QFD or Quality Function Deployment is a set of tools and processes that effectively defines the customer’s requirements and converts them into elaborate engineering plans and specifications to produce products that meet those requirements. In simple words, QFD prioritizes the customer’s needs throughout the entire process of product development. QFD translates the Voice of Customer (VOC) or customer’s requirements into measurable product design targets and drives them through each level, from assembly through processing and final production. Following is a graphical illustration of the QFD product planning matrix or “house of quality” that shows how customer’s needs are directly related to the methods organizations can use to achieve those needs.
QFD was first used in Mitsubishi’s shipyard, and with time, it got adopted by companies like Toyota and its supply chain. It was the early 1980s when QFD was introduced in the United States by electronics manufacturers and automotive companies. Since then, QFD has gained acceptance and popularity and is now being used across the manufacturing, service, and healthcare sectors.
QFD Methodology
The QFD methodology is a 4-step process encompassing activities throughout the entire cycle of product development. At each phase, a series of matrices translates the VOC to design requirements for each system and component.
- The first stage is all about defining the product. In this stage, VOC is collected, and the customer’s needs and requirements are translated into product specifications. The initial design is based on the specifications and performance requirements of a particular product. The first stage may also include a competitive evaluation to analyze how effective the competitor’s product is at fulfilling customer’s expectations.
- The second stage entails product development. The crucial product characteristics are identified and translated into key parts and assembly features or specifications in this phase. Then, the functional requirements are described for each operational level.
- The third stage entails the development of the process. During this phase, the assembly and manufacturing processes are designed based on component and product specifications. So, this stage includes the development of the process flow and the identification of fundamental process characteristics.
- The last stage involves the Quality Control assessment of the process. So, before the product launch, the Quality Function Deployment process identifies the critical part and process features. Process parameters are decided, and appropriate process controls are developed and employed. Full production begins after the process capability studies are completed during the pilot build.
Why Implement QFD?
Smooth and effective communication is one of the most impactful factors that drive an organization to success. The QFD methodology is designed to efficiently communicate the customer’s needs to all the business operations within an organization, including manufacturing, quality, design, sales, marketing and production. This effective transmission of the VOC promotes intra-organizational collaboration while producing products that meet the customer’s perceived idea of quality and value. There are several other benefits to implementing QFD:
- Product development cycles get shorter
- Start-up costs are considerably reduced
- A useful tool for improving the quality of deliverables
- Besides improving product quality, QFD also facilitates the stabilization of the quality
- An environment of collective and teamwork is promoted
- A way to analyze how your product fares in comparison to that of your competitor
- Decisions and lessons are documented for future reference
- QFD allows the identification of the reasons behind the customer’s complaints and facilitates prompt and remedial actions
- Enables the identification of sales points that results in significant market benefits
The essence of the Six Sigma Green Belt training and certification lies in embracing the Total Quality Management System to deliver the products of the highest quality. Quality Management is essential not just to create the finest products, but also to exceed the customer’s expectations, which depend on the product’s perceived quality in terms of performance, robustness, and dependability. Quality Function Deployment is one such tool that drives the product design and production process with the primary objective of fulfilling the customer’s needs. In this light, the Six Sigma Green Belt training is the best way to understand the various factors that affect processes and quality.